- We work closely with our Asian partners who build machines and equipment to our quality guidelines.
- All builds are project managed by our skilled British team who monitor the manufacturing process and ensure all equipment is CE compliant.
- The machines when completed have inspection and testing done in Asia before onward despatch to the UK.
- We invite customers to see their machinery running and where possible we will do so with product.
- Travel itinerary in Asia for machine inspections can be arranged by Loynds.
- Be assured, we are always here to help with technical knowledge, spare parts, and any customer service that you may require.
- Machines will be shipped as standard back to the UK for further quality checks and final testing.
- If you require machinery on a short lead time we can arrange for the machinery to be shipped directly from Asia to you.
The Loynds Chiclet & Stick Gum Line is for extruding and shaping gum products into a stick form, like Wrigley chewing gum. With the addition of a drum breaker/sifter, the line can also be used for producing small chiclet type gum pieces. The output of the line is approximately 150kg per hour.


Interested?
Call: +44 (0) 1253 882 961
E-Mail: sales@loynds.co.uk
for more information.
Consisting Of:
- Gum sheet extruder, 300mm sheet, 11kW.
- Conveying.
- Powder spreader.
- 6-stage sheet roller, 300mm wide.
- Powder Vacuum unit.
- Gum strip scouring and sheet cutting machine.
- Scrap return conveyor.
- Conveying.
The chewing gum line begins with the extrusion of a gum sheet that is then conveyed and automatically powdered on both the top and bottom. After being powdered, the gum sheet is then reduced in thickness by a six-gauge roller unit and further conveyed to the automatic powder removal unit.
The gum sheet enters the scouting and cutting unit and is cut into smaller sheets; rollers create a chiclet/stick impression onto the gum. The sheets are then conveyed away from the machine and an operator will need to stack them so they harden, ready for wrapping. A refrigerated cooling tunnel can be used, if required. Once the gum sheets have hardened, they are then placed in to the breaking and sieving drum and the gum pieces will separate; any crumb webbing is removed.
To coat the gum pieces with sugar and glaze, we are also able to supply 1000mm coating pans.
Machine |
Capacity |
Power |
Dimensions |
Extruder | 300kg | 15.2kw | 1500mm x 700mm x 1300mm high |
Rolling | 300kg | 4.1kw | 2400mm x 750mm x 1200mm high |
Scouring | 300kg | 2.1kw | 1000mm x 780mm x 1150mm high |
Cutting | 300kg | 1.5kw | 1000mm x 250mm x 1420mm high |
Sieving | 300kg | 1.5kg | 2080mm x 750mm x 1420mm high |
Coating Pan | 45kg-90kg | 1.1kw | 1000mm x 1000mm x 1600mm high |
See the Loynds Gum Line in production:
Wrapping Machine for Stick Packed Chiclet Gum Pieces
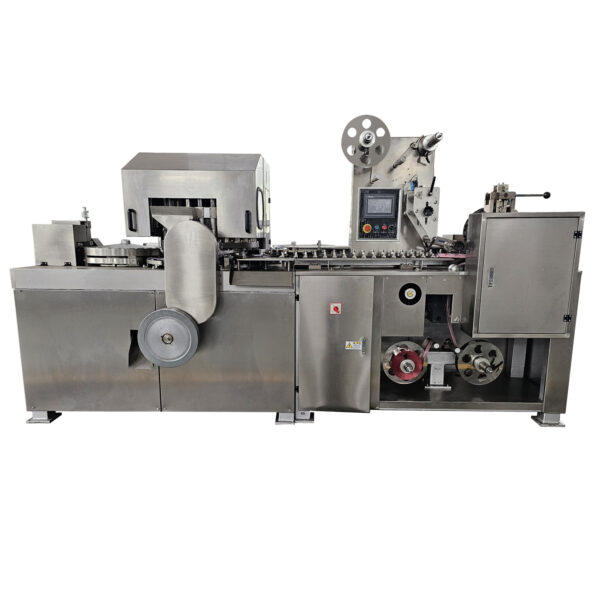
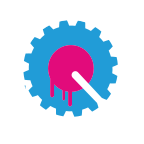
The FLM01 flat lollipop manufacturing machine is an efficient, customisable solution for industrial candy lollipop production, managing all stages from cutting the candy to wrapping, ensuring consistent qu...
ViewFlat Lollipop Machine Production System – FLM01
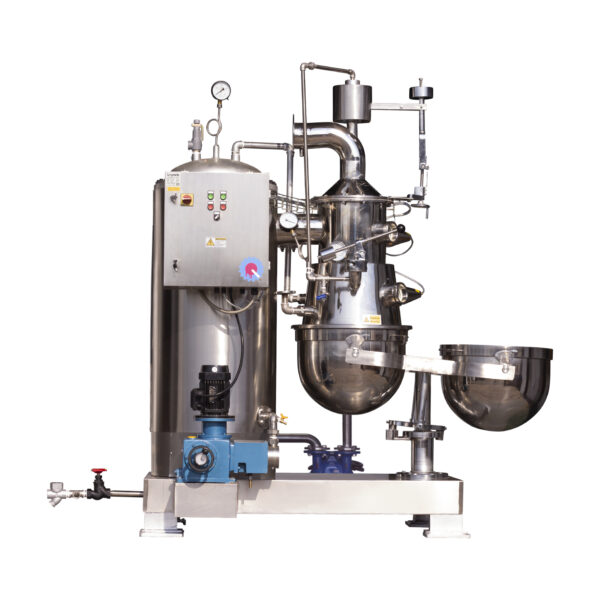
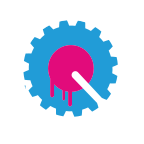
Our semi automatic candy vacuum cookers deliver high-quality boiled sugar or isomalt syrups, essential for high quality candy production....
ViewSemi-Automatic Vacuum Cooker for Industrial Candy Manufacturing – VC01
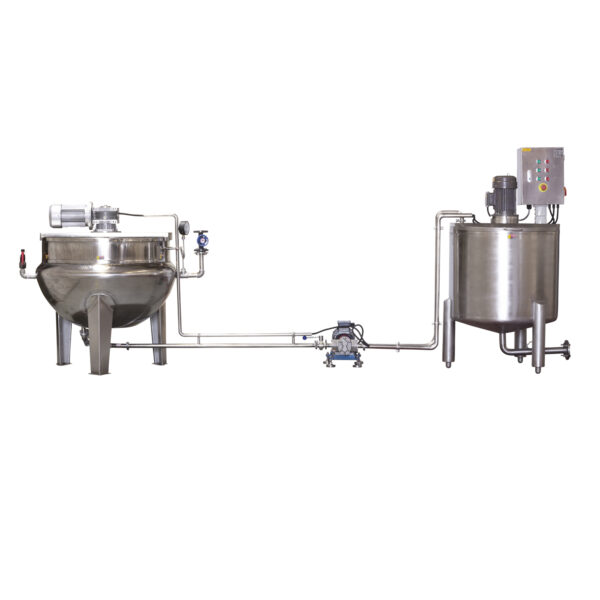
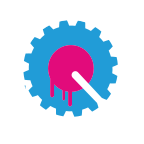
The Loynds Sugar/Glucose Dissolving System is a complementary system for candy manufacturing when using a vacuum cooker. Our system streamlines the sugar dissolving process, enhancing efficiency and produc...
View